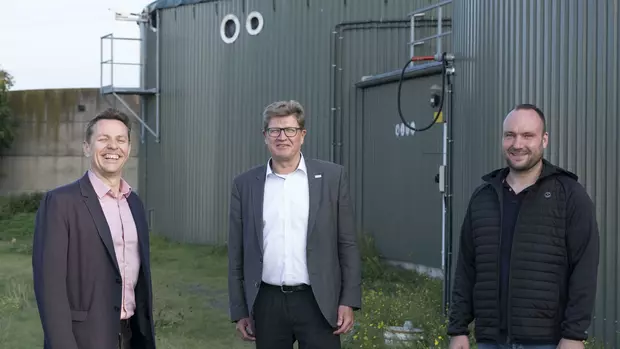
Since 2011, the biogas plant in Großen-Buseck has been producing a high-quality andCO2-neutral fuel. This is used to generate electricity and heat on site. A concept that continues to impress even after a decade.
Stadtwerke Gießen (SWG) is celebrating a milestone anniversary: its first biogas plant has been in operation for ten years. And extremely efficiently. At the time, SWG took a completely different approach to the production of the natural andCO2-neutral fuel than practically all other competitors. And today - a decade after commissioning - this unique approach is proving to be absolutely right.
As with many anniversaries, it is worth taking a brief look back. At the time when SWG began planning, politicians were discovering biomass as a source of energy. Thanks to lucrative subsidies, many farmers switched to energy farming. With all the excesses that such state subsidy programmes entail. In many places, maize sprouted from the ground instead of wheat, rye or barley. Hay became scarce. "It was clear to us from the outset that we would have to approach the issue differently," recalls Matthias Funk, Technical Director of SWG. As head of the district heating department, he was deeply involved in the project at the time.
Maximum efficiency in all respects
The fact that someone who actually deals with the generation and distribution of heat is driving the topic of biogas forward says a lot about the special approach. For SWG, there was never any question of only utilising biogas to generate electricity, as was customary at the time. The location of the farm on which it is situated is therefore crucial to the success of the small plant. "It's only 1.5 kilometres from the Klos family farm to our heating network in Großen-Buseck," explains Matthias Funk.
This proximity enables the economical operation of a combined heat and power plant. Such a unit converts the biogas into heat and electricity. And it is precisely this dual use that is the most important factor for the high efficiency of the overall plant. The scientific support provided by the Technical University of Central Hesse (THM) also plays a key role. "Our aim was to find the best substrate ratio. In short: as much liquid manure as possible and only as much biomass to be cultivated as necessary without reducing the biogas yield," summarises Matthias Funk. Because the more liquid manure the livestock farms can deliver from the surrounding area for fermentation, the less they have to spread on their fields. And the less maize and grass are needed for the fermentation process, the more land remains available for other important crops. "The THM team experimented a lot and changed parameters such as the temperature and the speed of the agitators to determine the best mixture," explains Matthias Funk. With success. Since then, farmer Dietmar Klos, who is responsible for the fermentation process, has been feeding the plant according to these specifications. He, his brother Marco, graduate engineer Besim Krasnici and SWG are the owners of MIT.BIO Biogasanlage Großen-Buseck GmbH, which was founded in 2011. Joachim Kauß from SWG is responsible for technical management.
Last but not least, clever details ensure that last bit of efficiency. In order to be utilised in a CHP plant, the biogas must be as cool as possible. In Großen-Buseck, it flows out of the fermentation tanks - the so-called fermenters - through a winding pipeline surrounded by cold groundwater. "We practically don't have to use any energy to lower the temperature to the required level," says Joachim Kauß happily. The SWG engineers also pulled out all the stops for the CHP unit itself and transferred a principle known as condensing boiler technology to the system: using an additional heat exchanger, they extract heat even from the exhaust gas. This increases the thermal efficiency from 51 to 57 per cent. All this led to a pleasing result: at the time, the biogas plant in Großen-Buseck was the most efficient of its kind in Germany.
As a regional energy service provider, SWG is naturally moving cautiously into new territory. In other words, although the preliminary calculations showed that the plant should in principle produce enough biogas for two CHP units, they initially only installed one. This was also to test whether the heat exchanger in the flue gas line could withstand the unusual loads. After a good year of absolutely trouble-free operation, a second, identical engine was added in 2013. This doubled the energy yield and earned the SWG subsidiary MIT.BIO the "CHP plant of the month" award.
Hard figures show just how much the biogas plant in Großen-Buseck contributes to local climate protection: Over the past ten years, almost 9.8 million cubic metres of biogas have been produced from materials that are expressly permitted under the Renewable Energy Sources Act. SWG used this to generate around 22.6 gigawatt hours of heat and around 19.7 gigawatt hours of electricity. This results in enormousCO2 savings. It amounts to a good 3,000 tonnes per year.
Always in top shape
Of course, the overall system only achieves its maximum efficiency when everything is working optimally. This is why SWG completely checks the two CHP units after 30,000 operating hours at the latest - i.e. approximately every four years. Particularly worth mentioning: In Großen-Buseck - as in all other CHP units - SWG uses a special engine oil. It ensures optimum lubrication of the units for more than twice as long. And it also extends the service life of the engines. They are usually replaced after around 60,000 operating hours. "The first engine has already undergone its second overhaul, has around 80,000 hours on the clock and is still running," says Joachim Kauß. Engine 2 is currently being overhauled. It has been in operation for 54,220 hours so far.
MIT.BIO also recently carried out a complete overhaul of the two fermenters, during which the walls were given a new coating. Residues were also removed from the floor. This also improves efficiency. This is because the agitator no longer has to whisk the viscous sludge layer that has grown over the years, which noticeably reduces electricity consumption.
The biogas plant in Großen-Buseck is a real highlight in terms of climate protection. With this plant, SWG is proving that you don't always need high technology to massively reduceCO2 emissions. In many cases, clever solutions from dedicated engineers are enough to significantly improve tried-and-tested concepts.